LINK TRADING RELIABLE PRODUCTION MANAGEMENT AGENT IN CHINA
NEED PRODUCTION MANAGEMENT IN CHINA?
- Truthful commission
- Professional production management in China
- Sourcing, quality control, and import services
- One-stop company for your products
- All-around business support
- Any industry
Production management entails the development of product strategy, decisions concerning the products, and marketing.
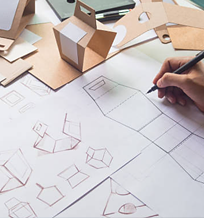
Production Design Selection
Firstly, production management starts with design and idea generation. Your product has to comply with certain safety standards and import regulations. We can help guide your design to meet these requirements. Plus, by performing value engineering and value analysis, we’ll be able to balance your product design features with your budget.
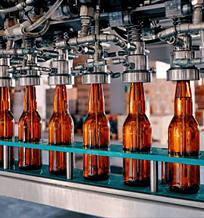
Production Capacity Selection
Choosing the right production capacity will directly increase or lower your profits. And so, as part of production management in China, we will deal with capacity. We will consider both short-term and long-term goals, and break-even analysis. Let’s skyrocket your business with perfect production capacity selection.
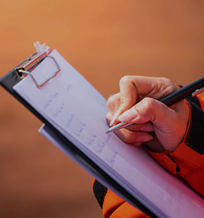
Production Control
Production control service compares production plan with how production is progressing in reality. Our agent will then analyze any deviations from the plan and correct them. Production control management also includes quality control and cost control. Link Trading will ensure that your products comply with quality requirements, and that costs remain economical. Interested in our production management services in China? Take a look at our factory audit and inspection services as well!
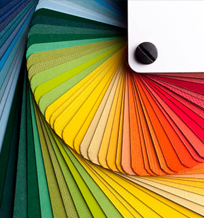
Production Process Selection
Our professional production management teams will also help select the suitable production process. This includes material handling systems, machines, technologies, and more. We will source the best manufacturer in China for your product. Also, we will settle on the production process most fitting to your requirements.
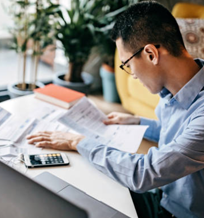
Production Planning
Production planning is another important part and service of production management. This includes routing and scheduling. Routing refers to the efficient flow of work, the steps of the manufacturing process, and operational sequence. Scheduling helps plan time and due dates. As a result, everything in production is planned out. Contact us today for professional production planning management in China.
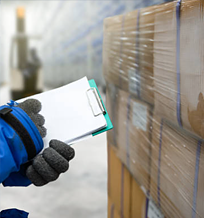
Inventory Control
As part of production management, inventory control is also examined. We make sure that there is no over-or under-production. Both problems will greatly affect your business. We ensure that materials are not spoiled and that your deliveries are not lacking. We will ensure the smooth running of your production in China.
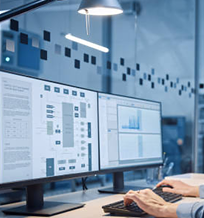
Production Analytics
We will analyze your production profitability, costs, output, and more. Also, we will inspect factory machinery and equipment as part of efficiency metrics. All our findings will be neatly organized into coherent reports for your viewing. Link Trading is your experienced production management agent in China. We are always happy to advise your business.
Fraquently Asked Question
Production management involves organizing, controlling, planning, and directing the production process. We work with you and the supplier to optimize workflow, costs, and timelines.
There are several components of production management in China. The process starts with design selection, factory selection, production process selection, production capacity, planning, control, quality and cost control, and more.
In analyzing your production and selecting the best strategy, we look at a few things.
We look at your requirements and your target customers. Then, we decide on the criteria of success and various metrics. Our professional managers will select the best production strategy.
The basic types of production processes are batch, continuous, and project.
Batch production is for small quantities of a product, such as a limited edition product. Continuous production is large-scale mass production with a series of operations and non-stop manufacturing. Project production is when one or two products are made at once, such as prototypes. We will assess the type of your product and demand, and choose the optimal process.
Production management optimizes the supply chain. Through it, business concepts are used to create products. Production management helps guide your manufacturing and importing process in China. With it, we will be able to lower production costs, procure materials, direct factory work, control quality, and increase your profits. Production management in China is vital for import success.
Our commission is 5-10%, depending on what services you request. Contact us today to get the exact quote.
We have been sourcing in China for 8 years, so our production management teams are very experienced.
Some challenges that may surface during production management in China include quality problems, output problems, cost problems, and management problems. Quality problems entail high defect and return rates. Output problems mean long lead times, unreasonable scheduling, overstocking, and understocking.
Cost problems involve low efficiency, idle personnel, and machinery. Further management problems are safety hazards and bad working conditions. Sourcingwise production management in China will ensure that all these problems do not affect your products.
Any other question?
Feel Free to contact us, We're always here
Examples of Industries We Can Manage Production For
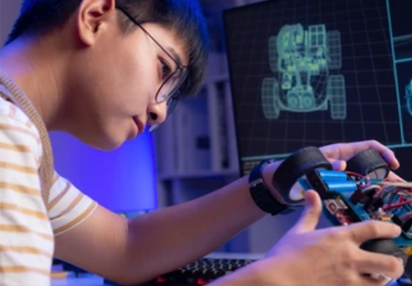
Whether you want to import electronic, plush, or educational toys, Link Trading will provide professional production management. We will optimize the supply chain, direct all processes, and ensure safety of the toys from China. We will also take care of inventory control. Let’s skyrocket your business with our production management.
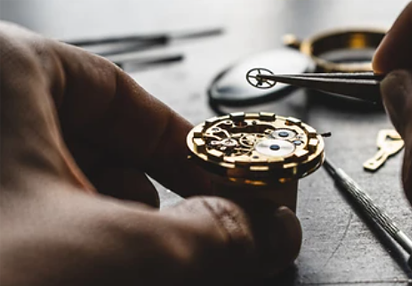
WATCH PRODUCTION MANAGEMENT
Are you importing elegant or waterproof watches? Contact us, and we will set up the ideal production for your goods. We will direct batch production or mass manufacturing depending on your requirements and market demands. We will also keep track of all timelines and due dates. Your production will always follow the planned schedule. To improve efficiency, your import delivery will be on time.
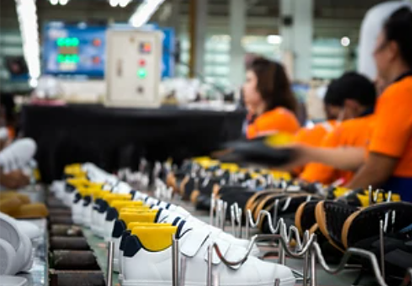
Link Trading will ensure the smooth workflow of your production process. We will source the best shoe manufacturer in China, perform an audit, and create a detailed and realistic plan. Your wholesale shoe brand is sure to profit with our cost, quality, and inventory control.
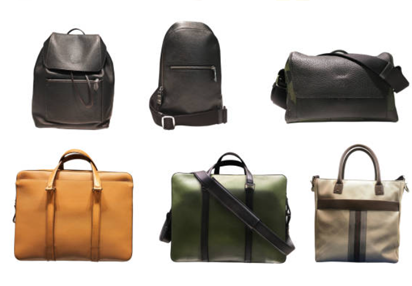
Why worry about production management when Link Trading is here? We will support your backpack production in China. Your comfortable and stylish designs will be efficiently made to boom your business. We will analyze your market, your costs and profits, and compliance with safety requirements. Our professional backpack production management in China will bring you success.
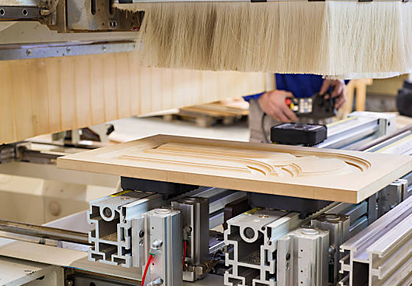
Furniture from China is a profitable and creative business. This is why we are offering our production management services to help your brand grow even more. By performing on-site control and value analyses, Link Trading will take care of the quality of your furniture. Your unique chair or table designs will secure a great spot on the market with our production planning.
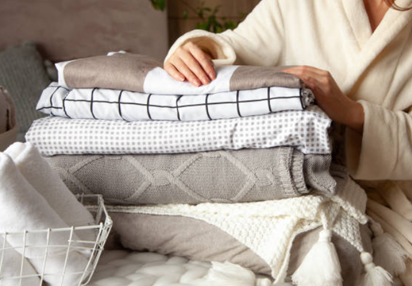
Blankets, as well as pillows and bedding, are another popular product for import. If you would like production management for your idea, we will help. We will balance output, quality, and cost. We will also make a detailed plan for all operations, sourcing, and import. Just rely on us for your production management in China.
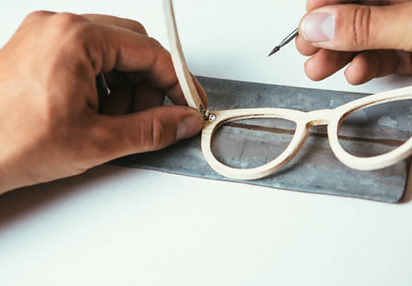
Do you need to import stylish sunglasses from China? Contact Link Trading ! We will find the best supplier for you. Also, our professional production planning will shield your business from problems. Any challenges that arise, our agents will plan corrective action against. All to protect the success of your sunglasses import from China.
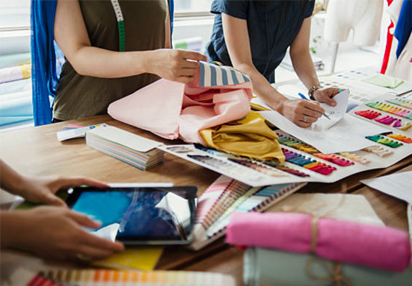
Clothes production is a large industry in China. A lot of clothes are imported from Chinese manufacturers all the time. This is why Link Trading specializes in production management for apparel companies. We can source, select the right process, direct, and control production, as well as working conditions. With our production management in China, your clothes import will prosper.
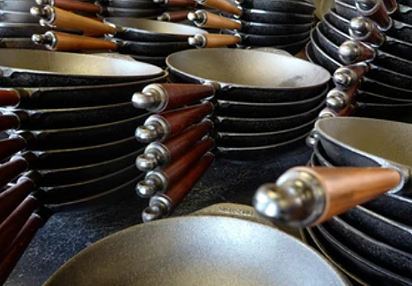
KITCHENWARE PRODUCTION MANAGEMENT
Pans, bowls, measuring cups, spoons—these are just some of all the kitchenware we can source for your business. Whether you need full support for production management or just specific services, Link Trading will provide everything. Our planning and control will streamline your kitchenware production in China.
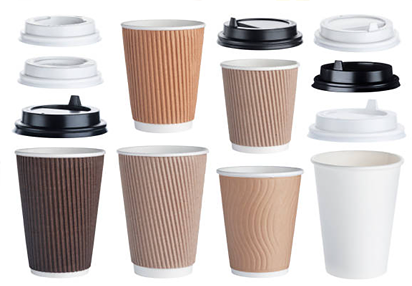
Link Trading will help you manage your production of paper cups in China. Any design—printed, double-wall, foam-surface—will be successfully sourced. Our professional production managers will create the perfect plan, balance all expenses, and control quality. Your paper cup production in China will boom your business.
The Most Reliable Production Management Agent In China
Production management is a responsible task. It oversees the entire production process, preparatory action, and analytics. To make the most out of your import, proper production management is critical.
Here is where Link Trading comes into play. We have extensive experience in many commercial industries. Contact us today and let’s talk about your product ideas!
Our approach centers on transparent business practices and support for our client. Your production management in China will be in great hands with Link Trading.
Production management entails many different services, steps, and processes. And we will take care of everything for our 5-10% commission.
We will start with your product idea and design, making sure that it complies with safety regulations. We will also ensure that production meets your budget plans, and proceed from there.
Then, we will source a factory in China for you, perform factory audits and inspections. If you already have a supplier, then we will advise on the production process and strategy. Analyzing the market, your budget, and your requirements, we can set up batch or mass production in China.
Our agents will calculate the most profitable production capacity, professionally balancing expenses. Your business is sure to prosper with our production management.
Production planning is another important step in management. We will figure out routing and scheduling. All the workflow operations will run smoothly and on time. If something happens and production goes off-track, our agents will plan to fix the issue in record time.
Of course, we will conduct extensive inspections. These include quality control, inventory control, cost control, and process control. Your products will always be up to standard without cost increases. And, your warehouse will never be overstocked or empty. Production management process control involves checking machinery, working conditions, and safety regulations.
Your production management in China is an all-around service from Link Trading . Supporting your import business is our #1 priority.
We are your one-stop professional production management agent in China. Let’s build a reliable business relationship to bring your brand success.
Contact us today for professional production management support.
Production Management: The Complete FAQ Guide
In today’s guide, you’re going to learn all the fundamental aspects about production management.
So, before starting any production process, you should read this guide.
Remember, production management also goes hand in hand with product inspection.
Let’s dive right in.
What is Production Management?
Production management
Production management aims to ensure that the right quantity and quality of goods are produced at a minimum cost and at the right time.
It applies management principles such as planning, directing, organizing, and controlling towards the production process.
What does Production Management entail?
Production management involves five main factors:
Plant
The plant is a fixed asset. It has to match the product needs; the worker, the market, and the company.
It is mainly concerned with:
- Safety of operations
- Perfect reliability and maintenance of equipment
- Layout and Design of offices and buildings
- The financial constraint
Product
Product is mainly a link between marketing and production.
A company must be able to produce a product to meet client demands.
In regards to the product policy of the company, an agreement should be reached.
This should be between the different functions on the below aspects of the product:
- Quality and reliability
- Performance
- Ergonomics and aesthetics
- Quantity and selling price
Process
The process is the method of producing a product.
When selecting a method, one should consider the following factors:
- Manufacturing costs
- Any maintenance required
- Safety
- Layout of plant
- Type of production
- Manpower skills available
- Available capacity
Program
This is the schedule/timetable of production.
It involves a schedule for purchasing, transforming, maintenance, cash, storage, and transport.
People
The production relies on people, and they vary in skills, attitude, and expectations from work.
For a company to make the best use of human resources, they have to ensure a good match between jobs and people.
With a good match,job satisfaction is guaranteed.
What are the Different Types of Production Management?
There are three main types of production management:
Job Production
Job production exists when one produces a single unit of a particular product.
The product is designed and produced according to the client’s specifications within set cost and time.
Its main distinguishing feature is the high variety and low volume of products.
Batch Production
A manufacturer is aware of the units of products the client wants and makes the right quantity.
Production takes place in batches.
Flow/Mass Production
This type of production focuses on specialization.
It is used to manufacture large volumes of a product.
Mass production is used to manufacture huge volumes of a product.
What are the Benefits of Production Management?
Production management is associated with the following benefits:
- Helps businesses to satisfy customers’ needs hence increasing their reputation, image, and goodwill. With a good image, a business can expand and grow.
- Helps a firm introduce new products into the market.
- Aids in optimum utilization of resources. Typically, production management facilitates the optimum utilization of resources such as machinery and manpower.
- It helps minimize the cost of production. It minimizes the inputs and maximizes the output, thus helping the company achieve its efficiency and cost reduction.
How does Production Management Work when Sourcing from China?
When a business outsources production to China, it employs the services of a Sourcing company/agent.
The company/agent is responsible for the production management.
For this, the Business works together with the agent to organize the development of products.
The firm discusses with the team specifications such as quantity, quality, budget, and sample products.
The agent then identifies trusted partners for the manufacturing process.
The client will show the factory’s photos, share certifications and other important documents with the agent.
These are mostly used in the Factory Audit process.
Once the factory verification is complete, the Manufacturer can procure raw materials and begin production.
The China sourcing agent will continue to monitor the production process to ensure all production management aspects are met.
What is Production Systems?
Production System
Production systems are the methods utilized in industries to create goods and services from different resources.
The methods include functions needed to gather the inputs, reprocess/process units, and deliver the goods.
What are the Components of a Production System?
Production systems are used in the manufacture of both tangible and intangible goods.
For a tangible good, this production system can be used in the goods industry, such as Food and Clothing.
For intangible goods, a production system is utilized in the service industry.
Even so, a production system consists of three main components:
Inputs
They include man-hours, machines, raw materials, parts/components, instructions, and paperwork.
Conversion Process
It includes the actual production process.
The operations can be mechanical, manual, or chemical. Also, operations transform input into outputs.
The conversion process entails supporting activities that support the conversion process.
Some of the supporting activities include purchasing raw materials, production control, and planning, receipt, storage, and materials issuance.
Other activities are testing products, work-in-progress, an inspection of parts, warehousing of finished products, quality control, etc.
Output
Outputs include finished goods, products, and services.
Production systems are likely to fail if this arrangement does not result in a desired level of outcome.
Note: a production system is a combination of inputs, conversion process, and output.
What are the different types of Production Systems?
There are three main types of production systems:
Batch/Mass System
Manufacturing of products is done in batches based on the client’s order.
Medium-scale production is allowed under this system.
Project System
According to this system, a single type of product is produced for clients.
All the resources involved in producing the product are brought only one time.
Continuous System
This is a physical flow of material.
It utilizes special-purpose equipment/machines to produce standardized products in large quantities.
How do you Classify a Production System?
You can classify a production system on the following basis:
- Size of the pant; small size plant, medium-size plant, or large size plant
- Type of production; batch/Job shop/mass production
- The physical flow of material; there is a manual, semi-automated, or automated flow
- Variety of jobs; there is more variety such as electronic/automobiles, one variety such refiner/oil
- Demand pattern/nature of the order; either an unstable or stable demand
What is the Difference Between Production Management and Product Development?
Product development is the process of building a product from an idea to the release in the market.
Production management is the process that centers on developing an existing product or bringing a new product to the market.
What are the Different Phases of Product Development?
Product development process
There are six different phases of product development, as shown below:
- Planning
- Concept development
- System-level Design
- Design detail
- Testing and refinement
- Production Ramp-up
Who is a Production Management Agent?
A production management agent acts as the intermediary between a firm and the Manufacturer of a product.
What does a Production Management Agent do?
A production management agent performs the functions of production management although they are outsourced.
Considering that a buyer cannot monitor their products’ production process, a production management agent oversees the whole process and reports to them.
What Characteristics make a Good Production Management Agent?
Below are the characteristics that make a good production management agent:
- Have the ability to provide positive motivation to your workers to keep a project running smoothly
- Exceptional at time management
- Good communication skills; the agent has to communicate their ideas/thoughts clearly to various audiences
- Ensure all activities fall within the quota/budget
- Oversee the staff to ensure that every person is on task
- Maintain sight of the production team’s goals
What does Production Management need to start working with me on my Product Development Project?
Production management needs information about a product design to begin working with the client on the product development project.
You should provide all relevant details about the product, necessary documents, and manufacturer specifications.
What are the Stages of Production Management?
Below are the stages of production management:
Production Planning
The team decides on issues such as when, where, and how production will be.
Production Control
The focus at this stage is on cost, floor, and quality control.
Improving Productions Management
This stage involves the creation of more efficient methods of producing a firm’s services and goods.
At what Stage should I involve the Services of a Production Management Agent?
You can involve the services of a production management agent at the production control stage.
Do this just so that the agent can visit the plant, perform a factory audit and oversee/monitor products manufacture.
Production management agent
How do I work with my Production Management Agent for the best results?
You can always work with a production management agent for the best results in the following ways:
- Offering them competitive/reasonable pay
- Treating the agent with respect through effective communication
- Delegating important duties so they feel trusted and respected
- Frequent communication
How much do Production Management Services cost?
There isn’t an off-the-shelf solution to production management.
For this reason, it is not easy to determine the actual cost of production management.
This is because several variables go into calculating the cost of a production management service.
Some agents include certain costs upfront; others have them as optional costs, while others don’t offer certain services at all.
It is therefore important to ask the right questions regarding production management costs.
So rather than asking what the service provider charges, find out what you’re getting as part of your production management quote.
What is ‘Man-day’ in relation to Production Management Billing?
Man-day is the measurement unit used to calculate the workload a production management team can complete in a day.
It allows businesses importing from china to calculate the costs and labor it takes to do production management.
How is a Contract with a Production Management Agent structured?
Below is how a contract with production management is structured:
- Contract establishes the roles of the production management agent
- Functions that are being transferred to the production management agent
- Period they are expected to handle their tasks
- The pay
- Non-disclosure agreement
- Rules that the production management agent has to adhere to
How do I pay my Production Management?
You can pay your production management agreed amounts between the involved parties.
Payment methods that you can use include PayPal, direct bank transfers, MasterCard, and debit cards.
T/T payment is also acceptable among production management companies in China.
Can a Production ManagementAgent help me deal with Production Issues?
Yes.
Quality control is part of the roles of production management agents.
The agent will perform inspections at different stages of the production process to ensure quality and safe output.
If during quality inspections they identify problems, the agent will help formulate an action plan to remedy the issues.
They will also recommend measures to prevent the same and other issues from emerging going forward.
Is a Production Management Agent an Intermediary/Middleman in Production Management?
In a way, yes!
Production management offers 3rd party services to China importers.
They act as middlemen between importers and suppliers to help ensure smooth procurement and quality control process.
They handle this on the ground in China, where the buyer is unable to reach.
What are the Problems of Production Management?
Some problems that are likely to occur during production management include:
- Quality issues
- Management problems
- Cost problems
- Output issues
Can my Production Management Agent Verify if my Manufacturer is Legit?
Since the production management agent is on the ground, they can visit the Manufacturer’s plant and determine if they are legit.
They can take pictures/videos of the place.
Also, they research information on the Manufacturer to determine if they fulfill all the certifications/regulations/have a good reputation.
Can China Production Management Agent Provide Recommendations for Reliable Manufacturers?
Of course, yes.
One way of finding reliable manufacturers in China is by relying on your production management agent’s recommendation.
These are people on the ground with experience and an extensive network.
They can help you find reputable manufacturers for your product.
How do I prevent bribery of Quality Inspection Agents during Production Management?
You can prevent the bribery of quality inspection agents during production management through:
- Emphasizing ethical compliance during the hiring process
- Offer competitive/reasonable pay for the quality inspection agents
- Audit the quality inspection agents to verify their conduct
- Rotate the inspectors to prevent excessively familiar relationships with the factory staff
- Prevent any integrity issues with policy, documentation, and training
Note: Always strive to limit the risk
What Kinds of Goods require Production Management?
Usually, you can perform production on all kinds of goods to ensure smooth production and adherence to quality standards.
While this so, certain products need production management services more than others.
Products with parts and components such as electronics and machinery are good examples.
Others include:
- FMCG, consumer durables
- Electronics
- Hardware
- Medicines
- Automobiles
- Alcoholic products
What is Reliability Testing in Production Management?
Reliability testing is done to improve the actual reliability of products or measure the expected reliability of products.
Typically, this test is utilized in the manufacturing process to test the specific production output.
What is Intellectual Property (IP) in Production Management?
Intellectual property in production management is the idea/concept developed by a buyer involved in the production/manufacture of a product.
How do I Protect my Intellectual Property during Contract Manufacturing?
You can protect your IP during contract manufacturing by making the manufacturer/supplier sign a Non-Disclosure contract.
Can my Production Management Agent help me Protect my Intellectual Property?
Yes, your production management agent can help you protect your IP.
They can do this by ensuring that the Manufacturer cannot share your business secrets with competitors.
Since they are on the ground, they ensure that the involved parties sign a Non-Disclosure contract.
They also make clear the penalties and general consequences for breaching the terms of the NDA.
A good production management agent will also avoid talking about your product with people other than the manufacturers.
Do China Production Management Agents provide Design/Engineering Services?
Product design and engineering
Most of the time, China production management agents do not provide design/engineering services.
Also, the production factories do not provide these services.
One must complete this process before going to the production management agents/production factories.
Factories work based on what is provided by the client such that any rework charges are passed onto the customer.
There is an exception, though, as a few companies do provide this service.
Such production management companies have in-house designers and engineers that can help design your product at a fee.
Other PM companies may request to outsource the design/engineering services, so you don’t have to rely on the Manufacturer for this.
Who owns all Intellectual Property when a Production Management Agent does Design/Engineering Work?
The buyer/contractor owns all IP when a production management agent does design/engineering work.
All the designs and work are part of the contract signed by the agent.
They do not retain the ownership of the material involved in the transaction.
What happens if some of the Design works my Production Management Team does lead to Production Issues?
Together with the manufacturers, the production management team can identify the root causes of the production issues, whether the specifications or the quality.
From there, they can work on a plan to standardize the sources for their raw materials/components/resources.
How do I Certify my New Product?
Certification of a new product takes four steps:
- Application; during this time, there is testing of the new product
- Evaluation; the test data has to show that the product meets the qualification criteria
- Decision; a second review of the product is done, and it must concur with the evaluation
- Surveillance; while in the marketplace, does the product continue to meet the qualification criteria
Do I need to share my Design with my Production Management Team before Sending it to the Manufacturer?
Absolutely, yes!
You need to share your Design with the production management team before sending it to the Manufacturer.
This is because it is good for them to know what they are working with and ensure a seamless production management process.
The production management team should not be oblivious to what the buyer is looking for.
They get the Design and then share it with the Manufacturer who makes samples and the final products.
Note that to avoid issues of the production management team sharing the Design with competitors; it is best to draw a Non-disclosure contract.
Is it true that Hardware startups run into problems when launching new Products from China?
Yes.
Hardware startups can run into problems when launching new products from China.
They experience problems preparing and managing mass production, thus experiencing delays or going over budget.
These startups often are optimistic about the capabilities of Chinese manufacturers.
Also, they are optimistic about the readiness for production of the company’s new product design.
They fail to see any risks, do not challenge reassurances and predictions, and do not ask for the help of people with experience.
Their focus is getting into the market and increasing their product ROI, and this is not possible.
How do Quality Inspections work when Manufacturing in China?
Product Inspection
Product quality inspections are done before your product leaves your Chinese manufacturer/supplier’s factory.
Doing this prevents any quality problems down the line.
There is an inspection on-site of any manufacturing plant/factory in China.
Also, there is a post-production inspection.
The product inspection report is even delivered to the buyer on the day of the inspection.
Who assumes Liability for Product Defects occurring after a Quality Inspection in China?
A buyer assumes liability for product defects occurring after a quality inspection in China.
Usually, quality inspection agencies have a cap on their liability if there are clear signs of negligence in handling their work.
However, this cap is small, so it does not make sense to sue the inspection agency.
This situation can only change if a buyer books several inspections annually via a quality inspection agency company.
In such a case, the agency can negotiate for a high liability, forcing the company to contract liability insurance.
Note: It is always better to work with a company with a liability insurance policy or contract insurance for your products.
What Happens if an Inspection is Failed for my Product?
There are several options after a failed inspection for your products:
- Ask the Manufacturer to rework the products
- Sort the defects
- Ask the Manufacturer for discounts and ship the products anyway
- Refuse the goods (rare)
- Ship the goods anyway
- You can re-inspect your products to ascertain that they are either good/poor quality before shipment
Will the Quality of my Products be Perfect following an Inspection?
Product quality inspection cannot guarantee 100% perfect quality.
Typically, a product’s quality originates from the original Design, the production processes, the inputs used, and other factors.
Inspections help you find quality issues very early enough and reduce risks to make a difference.
Please note that you need to do work at an earlier stage with reliability testing, product design, and controlling risks in the supply chain to guarantee better quality.
How long does an Inspection Project take?
The majority of inspections are done in a day.
Other times it takes longer depending on the complexity of the work and the number of products.
How do I start an Inspection Project with my Production Management Team?
To start an inspection project with your production management team, you need to plan on several factors such as:
- When they can visit the site
- Products that will undergo inspection
- Day of the inspection
- Costs that will be incurred
- Safety regulations or certifications that have to be met
What Types of Product Inspections do I need for my New Product?
Product Inspection stages
For new products in the market, you have to ensure that they are of high quality.
One way of doing this is through inspecting the products.
Some types of product inspection are:
Production Monitoring Reporting (PMR)
PMR is a report of on-site production monitoring.
It is done to catch any production issues early on and tackle them.
It is also done to give detailed feedback on production process, production quality, and subcontracting cases.
It begins from the start to finish of the production process.
Similarly, it can be done during some production processes.
Some of the things to check for are:
- Defects
- How manufacturers repair rejects and how they prevent these problems in the days to come
- Conduct safety and function tests
- Are guidelines on the way to conduct production in place
- Are your specifications respected on products, packaging, and labeling?
Inspection During Production (DPI)
This is an on-site production inspection done to give a supplier and yourself feedback on production quality.
It involves the inspection of components from semi-finished to finished products.
A DPI can give the factory staff feedback that they can rely on to make any corrections.
You can use it if you are 98% sure that the factory staff cannot consistently produce your stated quality standards.
It is best to conduct this inspection on the first finished products.
Doing this helps catch any problems before they become full-blown.
You can also pick up samples during this time to conduct laboratory testing of your products.
Some of the things to check for are:
- Visual defects
- Product-specific checkpoints
- If your specifications are respected on products, processes, packaging, and/or labeling
Final Random Inspection (FRI)
This is an on-site product inspection monitoring the conformity of production to your specifications.
It happens once production has been completed, and the goods are ready for shipment.
It is also referred to as pre-shipment inspection.
It is a good test if you fear releasing payment and receiving a batch of products you can’t use or sell.
FRI is like a last line of defense.
Some of the things to check for are:
- Visual defects
- If your specifications are respected for packaging, labeling, and products
- If an order is within acceptable AQL limits
- Product-specific checkpoints: function and safety tests
Full Production Check (FPC)
This inspection checks the quality and quantity of a whole production batch at the supplier’s facility before shipment.
This inspection takes place at a factory so that if there are issues, they are corrected immediately.
Since a supplier may sometimes not send a batch of products that meet the market’s requirements for different reasons.
It is only better that a technician checks the full quantity piece by piece.
FPC takes 2-8 days before shipping once the production is over.
Some of the things to check for are:
- Product-specific checkpoints
- If your specifications are respected on the packaging, labeling, and products
- For visual defects
Packing and Loading Supervision (PLS)
With PLS, a technician confirms the packing used for order unity and supervises your shipment loading on a truck.
You have to send a technician at the time of loading to avoid the associated risks.
It protects buyers from unscrupulous suppliers.
They can make mistakes in the quantity of products declared or mistake on loading products or swapping the products before shipment.
A technician is sent a few hours before goods are loaded or when 100% of a shipment is packed.
You can check for:
- Condition of the truck/container
- Supervise the loading activity
- Check the packing and count the number of pieces to ship
- Check some of the products taken randomly to detect dishonest behaviors
What is Acceptable Quality Limit (AQL) for Product Inspections?
AQL is the maximum number of defective units over which a batch can be rejected.
It is the acceptance sampling standard as shown in the ISO 2859-1 standard.
During product sampling, AQL is used as a standard to determine whether a product batch passes or fails the inspection.
Is a Factory Audit Necessary when Looking for a Manufacturer for my Product?
A factory audit is necessary when looking for a manufacturer for my products.
This audit is necessary for manufacturers to come up with quality final products.
It is also the question of whether a factory can produce your products in time.
In essence, a factory audit helps a buyer understand a plant’s weaknesses and strengths.
What is Quality Consulting?
It is the process of reducing a buyer’s quality risks in a preventive manner.
Quality consultants establish processes that are better-controlled, leading to more consistent quality products.
Quality consulting reduces unexpected delays by lowering costs.
What are Supplier Background Checks?
Supplier background checks are inspections done to assure a client that a possible supplier is not a scammer.
It helps check if a supplier’s story is straight, is a good match for your Business, or gives competitive pricing.
Do I need to run Supplier Background Checks?
Of course, yes.
If you fear a potential scam or employ a middleman posing as a factory, you have to run a background check to produce your merchandise.
What are the average Production lead-times when manufacturing in China?
Production lead-time is the duration of the placement of an order and when the order is completed.
The average lead-times when manufacturing in China depends on several factors such as supply and demand (volume ordered) and the industry.
Even so, the average manufacturing lead-time can be between 30-60 days.
Manufacturers have to make purchases of materials and components from subcontractors as they only maintain a minimum amount.
Manufacturers must set a production time not shorter than 30 days to avoid these problems.
Where can I get a Good Production Management Company in China?
You can get a good production management company in China from:
- Recommendation from acquittances
- Alibaba/E-commerce platforms
- Online/Google
- Trade Fairs/Exhibitions
What are the Applicable Tests for Products I Manufacture in China?
Laboratory testing helps ensure that your imported products are safe and that they comply with the relevant standards/regulations.
- CA Prop 65 test
- ASTM test
Other specifics are conducted based on the type of product.
Your production management agent should be able to advise you on this accordingly.
What is the Difference Between Mandatory vs. Suggested Tests in Production Management?
Mandatory tests are tests that products must undergo to show that they comply with the recommended quality and safety standards.
Suggested tests are those that specific clients/companies require a buyer to pass their products through.
They are not mandatory as buyers have the conducting them or not.
Do I need to Test Every Single SKU when Manufacturing in China?
When manufacturing in China, you have to test every single SKU.
Even if you have two different SKUs with the same components or materials, you must test them.
Having a reasonable testing plan can cut costs by over half while keeping the risks down.
Are Production Management Agents the same as Sourcing Agents?
Production management agents can handle similar jobs as the sourcing agents.
They work on the ground, sourcing products from different suppliers.
They keep an eye on the production line, ensuring the production of high-quality and standardized products.
Can my Chinese Manufacturer help with all of the Production Management Steps?
Yes.
Your Chinese Manufacturer can help with production management using delegated staff in the factory.
However, it is not usually advisable to use manufacturer PM services as results may be biased.
What is Break-even Analysis in Production Management?
Break-even analysis is a tool utilized to evaluate business performance in terms of costs.
In production management, break-even analysis is the number of units required to cover total costs.
What are the Main Advantages of an Effective Production Management Solution?
When you implement several basic principles of production management, you are likely to enjoy several benefits, as shown below:
- You will build a good reputation within a particular market
- Improves one’s ability to develop new products and bring them into the market very quickly
- Reduction in a company’s overall cost, product management enables one to reduce costs at each stage of the production process
- Firms achieve a competitive edge in the market; hence they grow far more quickly. Embracing the principles of product management means that firms can keep a tight lid on costs.
- Companies that implement effective production management solutions can meet their customer’s needs while keeping the costs low.
What are some Production Management Challenges that I Might Face?
Communication challenges; if a buyer cannot communicate effectively with the agents on the ground, there could be several product specification errors.
How can Production Issues Affect my Supply Chain?
Several production issues can occur during the manufacturing process.
- Supply chain interruptions
- High on-hand inventory
- Long lead times
- Poor quality
- Cost problem where is low efficiency
- Management problem
Can I track Production in China? How?
You can track production in China.
One checks the factory/plant’s capacity during the audit.
Through this, they ensure that the production firm can make the order in a reasonable time frame.
In addition to the supplier’s forecast, clients add additional 2-3 weeks of padding.
If it is a new factory/product, the buyer can send an inspector to the place during production.
Through this, a buyer can check for the production status and product quality.
They can also check whether the complete order is manufactured in the approved manufacturing plant.
In essence, a buyer can utilize project management mechanisms to track the advances in production.
Is Production Management easy if I Several Orders with Several Suppliers?
Production management is not easy if you make several orders with several suppliers.
It requires a production manager to organize a good plan so that the different suppliers bring their products to a central location.
Keeping inventories is equally difficult.
There could be delays when bringing all the products from the suppliers to a central location.
What is the Importance of Communication during Production Management?
Communication is key to successful production management.
Here is the importance of communication during production management:
- Communication during product management helps keep all the involved parties/stakeholders informed, so there is no breakdown.
- It helps facilitate coordination. With good communication, there is a smooth flow of instructions from customers down to the factory floor.
- Communication functions as the foundation for planning and decision making
- It helps to carry out all of the production management functions
- Communication increases managerial efficiency
What Criteria Should I Keep in Mind while Selecting a Production Management Service Provider for my Business?
Below are the criteria for selecting a production management service provider for your Business:
Reputation/Brand Image/Familiarity
The production management service provider should have a good reputation.
A firm with a reputation based on track record is an excellent choice.
Experience
The chosen firm should have a wealth of experience providing these services.
A long experience shows that the company has been in operation for a while and is familiar with this service provision.
Price
A company that provides competitive costs/prices is more likely to be chosen by a client for their Business.
English language Proficiency/Languages
The production management service provider should be proficient in the English language or other languages.
Communication is a key aspect of production management; if a client cannot effectively communicate with the service provider, there will be several problems/consequences.
Does effective Production Management help Reduce Manufacturing Costs in China?
Absolutely!
Effective production management reduces manufacturing costs in China as one reduces time, resources, and human capital.
As such, you improve the efficiency of the manufacturing process and the productivity of the workers.
It reduces manufacturing costs by eliminating any errors that could arise.
When there are limited errors, a firm spends too little on quality control, lowering the manufacturing cost.
It reduces inventories.
There are limited delays; things move fast, facilitating a speedy manufacturing process.
Besides, with effective production management, a firm does not have to spend a lot on warehouse space because they produce the exact amount they need.
Effective product management minimizes manufacturing costs by minimizing input and maximizing output.
Is Production Management possible when Sourcing from Alibaba Suppliers?
Yes.
Production management is very much doable even when you buy from Alibaba.
After all, the manufacturing service you’ll receive from Alibaba suppliers is still the same all over China.
With years of experience in the industry, Link Trading offers perfect solution when sourcing for products from China.
In case you have any questions about production management, feel free to contact Link Trading team.