Link Trading
Your Most Reliable Product Inspection Company In China
Why Link Trading?
- Transparent business
- Protect from supplier scam and black commission
- Professional product quality inspection
- Thorough shipping preparation
- Reduce import risks
- Competitive, truthful rates
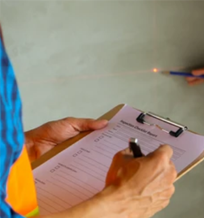
Pre-production inspection
Pre-production inspection lets you control production from the start to avoid risks. Link Trading will test the materials, facilities, machinery, and the readiness of the supplier. We will ensure that you and the supplier are on the same page. Also, check the quality of raw materials and parts.
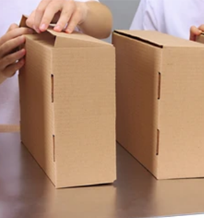
Post-production inspection
Our post-production inspection service happens usually just before shipment. Here, we will ensure that product quantity and quality are in order. All your requirements, function and safety tests will also fall under our strict inspection. Finally, Link Trading will check whether your goods have been packaged and stored well.
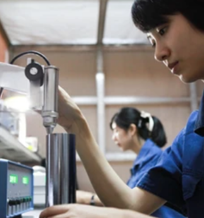
In-line inspection
We will monitor the production status for you. This will make sure that your goods are made and shipped on time. We will not only inspect production speed, but also quality of work. Furthermore, Link Trading will examine that the supplier is following your specifications, as well as production safety rules.
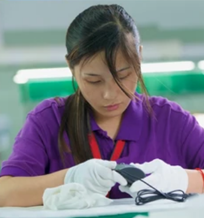
Piece-by-piece inspection
Piece-by-piece product inspection in China means that our inspectors will check each product for quality. Usually, 2-10 % of products are examined randomly. However, this service ensures inspection of everything. This is perfect if you have high standards or a high-stakes product like hospital gear.
Fraquently Asked Question
We have 8 years of experience in product inspection, so you can be confident in our professionalism and knowledge of the field.
This depends on what type of inspection service you choose.
In pre-production, we will go to the factory and examine raw materials.
During in-line inspection, we will test products at various stages of development.
During post-production inspection, we do the following. When the goods arrive at a warehouse, we will open random boxes for each type of product. This way, the supplier won’t be able to hide bad products somewhere in the back. Then, we will perform tests, record results, and take photos or videos for you. All this is included in the final product inspection report. Finally, we examine packaging and replace it if necessary.
Upon inspection, if we find goods of unacceptable quality, we will call the supplier and return the products to them. Usually, Chinese suppliers take responsibility for this and cooperate. However, sometimes they do not. In this case, Sourcingwise will deal with everything and protect your investment with our contract. You can always count on us!
You can simply contact us any time! As we work together, you will need to tell us some things you want us to inspect. For example, your quality standard, the quantity breakdown, description of your desired packaging, and any special requirements. Sometimes, it is also helpful to provide a sample of your perfect product if you have already made it. If not, no worries! We will help you, but our team would need details of your requirements and wishes.
If you choose to source with us, asking us for product inspection services will make the process easier for you.
We can also do process control to ensure that processes within a company are functioning correctly. For example, we can examine whether the machines are operating correctly, producing products accurately. Process control also checks that a manufacturer is performing at target output level—meeting production speed requirements.
Yes, of course! This is part of pre-shipment or post-production inspection. We will ensure that your products are packed and packaged properly, and ready to be shipped!
A control plan is a document that describes various measurements, inspections, quality checks or monitoring of processes required at each stage of production. We can develop this together and our specialists will conform to it.
We can perform product inspection in any industry. We constantly learn more and expand our knowledge of different products and fields. Below, you can look at some examples of common industries we can inspect products in.
Any other question?
Feel Free to contact us, We're always here
Industries We Can Perform Product Inspections For
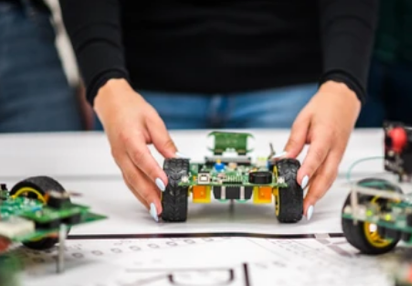
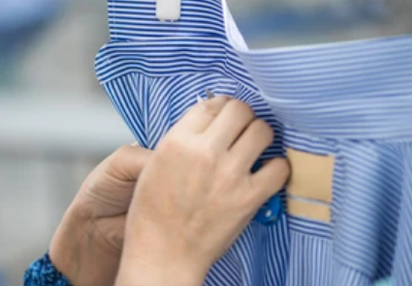
If you are a designer or clothes business, we can help you source and inspect apparel in China. We will examine both the start material and the finished product. Here, we would look for various fabric defects, proper garment labelling, pattern continuity, stitching, as well as toxicity of dyes and so much more. Everything to suit your product quality requirements!
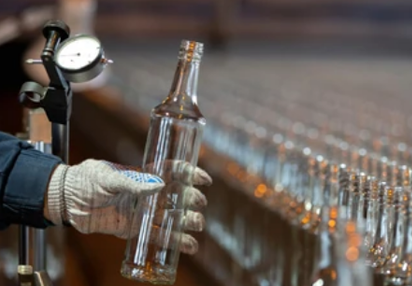
GLASS BOTTLE INSPECTION IN CHINA
Glass bottles and containers are used in many industries, such as food, cosmetics, beverage, etc. We can inspect glass bottles using illuminators, checking opacity, thickness, colour. We can also examine the strength of glass and how it shatters. Link Trading will take care to ensure high quality of your glass bottles.
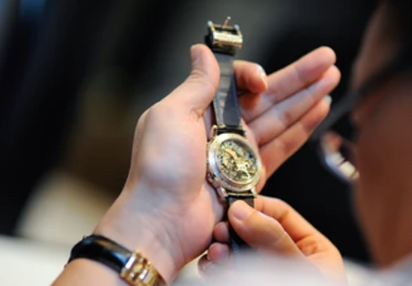
WATCH INSPECTION IN CHINA
Link Trading will help you source the perfect watch supplier in China. Moreover, we will inspect everything for you. We will examine time-keeping accuracy, scratch resistance, lifetime, and drop-test results. If your watches or clocks are waterproof, we will inspect all aspects of that as well.
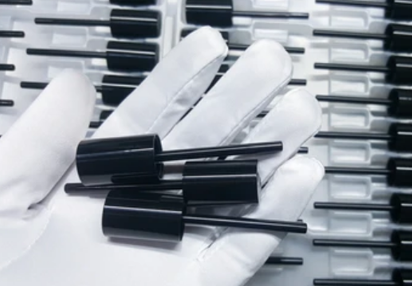
Beauty products, fragrances, self-care products, hygiene products—all these go under cosmetics. This is an especially large industry and quality here has high stakes. At Link Trading, we pay careful attention to product inspection for this category. We will examine clinical trials, toxicity, allergies, compliance with the EU Cosmetics Directive or the US Safe Cosmetics Act. All to ensure the safety of your products!
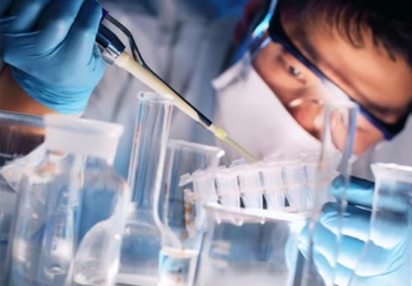
CLEANING PRODUCTS INSPECTION IN CHINA
Cleaning products include detergents, disinfectants, waxes, polishes, and more. These products are used to clean houses and offices, necessary everywhere. This is why we have trained inspectors for this industry as well. Link Trading employees will test shelf-life, performance claims, environmental effects, microbiological testing, and user safety. You can be sure of the quality of your cleaning products made in China.
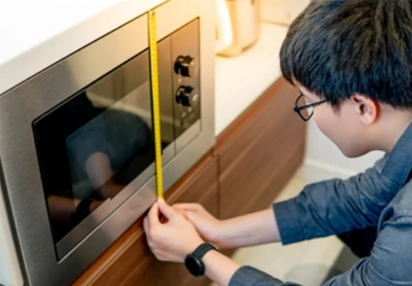
HOME APPLIANCES INSPECTION IN CHINA
Is your brand selling refrigerators? Microwaves? Kettles? Vacuums or dishwashers? We will source and inspect the right manufacturer for you! All these household appliances are different, so they will be tested differently. However, the general focus will be function and safety. For example, inspection may include electrical connection, power leakage, and sensitivity of dials.
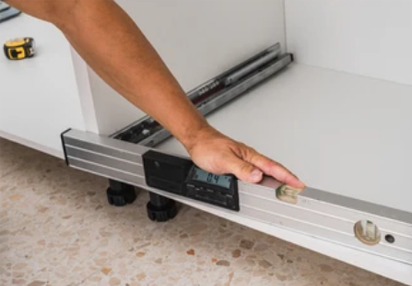
Manufacturing furniture in China is a great investment. And we will source the best materials and factories for you. Rest assured that your requirements are followed. During and post-production, our inspectors will perform drop tests, stability, symmetry, endurance, weight checks, and more. You will receive the perfect furniture you had in mind.
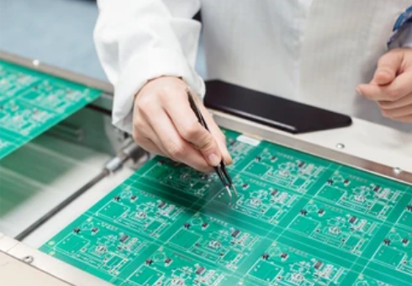
ELECTRONICS INSPECTION IN CHINA
China manufactures a lot of the world’s electronics, including mobile phones, computers, and more. So, product inspection for electronics sourced in China is important for many companies. We can inspect analog, digital products, radios, cameras, laptops, printers, etc. Product inspection includes power consumption, memory size, current leakage, frequency, and other checks.
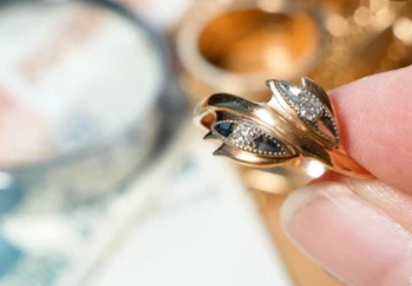
If you manage an accessories brand and want to provide high-quality jewelry, Link Trading has got your back! We have trained professionals that will inspect the appearance and functionality of products. Are the coatings and platings uniform? Are proper materials used? Is clasp performance and tensile strength sub-par? You will see all this information in our product inspection report.
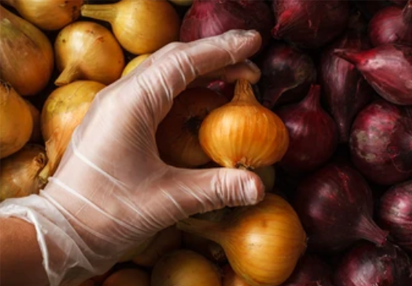
FOOD INSPECTION IN CHINA
A large amount of food and agricultural products around the world are made in China. Thus, we took the responsibility of sourcing and inspecting food from Chinese suppliers. Shelf-life, allergies, chemicals, infections—all will fall under our careful eye to deliver the best-quality foods for your business.
The Most Authentic Product Inspection Audit In China
Our services are built on transparency and trust with our clients. And so, we have undertaken the mission of sourcing making sure that you get the best production possible. Product inspection services in China are our way of protecting your goods.
Product inspection will help you save costs and time by catching bad products and preventing re-works. Presently, around a third of all products made in China must be re-worked. Such a supply chain has lots of room for improvement, especially for businesses sourcing on a large scale.
This is why product inspection by Link Trading is a great solution for your production. It will help lower the re-work rate. During in-line inspection, we can detect sub-par products and get them fixed or remade at once.
Also, you will avoid regulatory violations and build a fantastic brand image by having product inspection. This is because your customers will get only high-quality goods. Less returns, better company reviews!
Lastly, quality products are less likely to sustain damage during shipping. Quality products are in perfect condition, able to take loading and packing stress.
Inspection, testing, advisory, training, and quality assurance all create trust and efficiency across the supply chain.
Some types of inspection in manufacturing include pre-production, in-line, piece-by-piece, and finished product inspection. The procedures vary depending on your products.
Usually, we test some or all products by closely inspecting them and performing various tests. Link Trading checks appearance, function, and safety. We ensure that the product parameters meet your requirements, import directives, and government acts.
With us, your production will be looked after starting from raw materials inspection, and ending with packaging checks and loading supervision. Together, we will develop a control plan, quality checklists, and more.
Our trained professional inspectors are knowledgeable in any industry. What’s more, we always expand the range of industries we can provide product inspection in China for.
We take 5-10% transparent commission. And you can be sure that no negotiations happen behind your back. We value your business, trust, and growth.
Inspection and quality control in manufacturing ensures prosperity for every business.
Product Inspection: The Ultimate FAQ Guide
Whenever you’re importing from China or any other country, product inspection is a critical quality control (QC) process.
That’s why today, this guide will answer all questions you have about product inspection.
By the end of this guide, you will be an expert in product quality inspection process – keep reading.
What is Product Inspection?
Product inspection
Product inspection is the checking of goods to ensure that they are in conformity with a buyer’s specifications and requirements.
It is a quality control process that focuses on a product’s appearance, construction and basic function.
Product inspection is a key component of quality control.
The process allows you to verify a product’s quality at different stages of production, preventing quality problems.
What is the Purpose of Product Inspection?
The purpose of product inspection is to identify and sort out any defects in a product’s quality.
Inspecting a product earlier in the production process also helps identify any quality issues before they affect the majority of an order.
Product inspection ensures that goods are safe for use.
It also reduces the number of complaints from buyers owing to defects, thus building the manufacturer’s reputation.
What are the Advantages of Product Inspection?
Product inspection helps manufacturers figure out defects during the initial production process.
This helps them make necessary changes to ensure the end product is of good quality.
It also reduces the number of complaints from buyers.
Manufacturers gain customer loyalty when their products are of good quality.
Inspection reduces the amount of time used in production as repeated production of defective goods causes a delay in production.
Buyers benefit from product inspection because they can verify a product’s quality at the source, and they do not have to pay for defective goods.
Is Product Inspection the same as Product Testing?
Product testing
No.
Product inspection is the checking of goods, making sure they conform to your specifications and requirements.
On the other hand, product testing involves testing products against specific standards or regulations in a certified laboratory.
While carrying out testing, a representative sample or a few units of a product is adequate.
However, with product inspection, inspecting a representative sample is adequate, but a buyer may choose to inspect the entire lot size.
Also, a buyer may opt to inspect the entire lot size when the order is small.
An entire lot may also be inspected when the buyer has been experiencing recurring and widespread quality issues.
What is the Difference between Product Inspection and Quality Control?
Quality control is the process of managing a product’s quality to meet a desired standard.
Product inspection is a part of the quality control process, aimed at identifying the quality in a product.
Inspection helps suppliers/manufacturers detect defects earlier in the production process and remedy the situation.
Quality on the other hand is built into a product and cannot be added after production.
For example, using substandard raw materials leads to the production of low quality goods.
The quality of those goods cannot be remedied by inspection.
What are the main Types of Product Inspections?
Product inspection stages
There are five main types of product inspection:
Pre-production Inspection (PPI)
PPI takes place after a purchase order has been made.
A quality inspector visits a supplier’s site to evaluate the quality of raw materials, components and other plans for the manufacturing process.
Retailers use PPI’s to ensure that their suppliers are using the raw materials and components specified in the contract.
First Article Inspection (FAI)
This is carried out once production has started.
Quality control inspectors inspect the first units.
They do this from both the factory floor and design documents to ensure the product matches the specifics set out in the design documents.
FAI’s also verifies whether the requested processes are being carried out or not.
Most purchase contracts require retailers to carry out FAI’s.
During Production Inspection (DPI)
The DPI takes place once 20-50 percent of the units to be produced have been completed and packed.
A Quality Control inspector verifies the production and quality plan, inspects storage conditions, and conducts reliability and safety tests.
DPI’s are useful as they ensure that the goods in production correlate with the samples received.
Pre Shipment Inspection (PSI)
A Pre-shipment inspection is also known as the Final Random Inspection.
PSI’s ensure that the products have been manufactured to your specifications and packed as required by your purchase contract.
This type of inspection is only performed once manufacture is complete, and at least 80 percent of your order has been packed.
Container Loading Inspection (CLI)
A container loading inspection takes place at a supplier or forwarder’s china warehouse.
QC Inspectors supervise the loading of shipping containers to certify that a buyer’s order has been packed correctly.
Is Inspection necessary for my Product Type?
Yes.
Carrying out product inspection is necessary to ensure your products meet your desired standards and requirements.
Product inspection is an essential element of quality control.
You are able to protect your investment and avoid quality issues when you carry out product inspection.
Who can conduct Product Inspection?
A manufacturer may have internal Quality Control staff to carry out inspections.
However, it is easy for factory staff to misunderstand your requirements.
There are firms that specialize in carrying out inspections.
You can opt to hire a 3rd party product inspection and factory audit company to get reliable results.
You may employ inspectors full-time to inspect your products.
You may also decide to inspect the products yourself, according to your standards and requirements.
When should I conduct Product Inspection?
QC inspection during manufacturing
Carrying out product inspection depends on your requirements.
You can conduct product inspections at any stage in the manufacturing process.
However, it is prudent to conduct inspections before, during and after production.
Most quality control professionals recommend the Pre Shipment Inspection (PSI).
The PSI occurs when your supplier has completed at least 80 percent of your order.
However, you are at risk when you conduct inspections after the completion of such a large percentage of your order.
You will not be able to correct quality issues that may arise at such a late stage.
You should therefore conduct product inspection before mass production begins, during production and before shipping.
You should also inspect the container loading process to make sure your order is packed correctly.
How many Product Units do you need to Inspect to get reliable Results?
When your purchase order is large, it is adequate to inspect a sample of units randomly.
If your order is not that large, you can opt to inspect the entire lot size.
Product inspectors normally examine 10-20 percent of the order.
This sample size is large enough to reveal any issues with the product.
Who can benefit the most from Product Inspection Services?
Both you and the manufacturer/supplier benefit from product inspection services.
Suppliers who carry out product inspections reduce production time by detecting defects earlier on in the production process.
They also get good reputations as suppliers who produce goods of superior quality.
You benefit by getting good quality products that are not a threat to your safety.
You also avoid paying for defective products.
What is a Product Inspection Strategy?
A product inspection strategy is a systematic guide that tells you how to conduct product inspections.
A product inspection strategy helps you get a clear look at your order.
The strategy also helps your supplier improve quality issues should they arise.
What are the Key Elements of a Robust Product Inspection Strategy?
The first key element of a robust inspection strategy is preparing for the product inspection.
You prepare for an inspection by obtaining and approving a golden sample from the supplier.
Your approval of the golden sample helps your supplier determine and understand your standards and specifications.
You also develop a quality control checklist in preparation for the inspection.
The checklist helps your product inspector know what you expect them to check during inspection.
The second key element of a robust inspection strategy is checking the production status.
Your inspector checks whether manufacturing is on schedule or whether you should expect some delays.
He/she visits your supplier and finds out the quantity of products completed and packaged.
They also check storage areas and the safety measures your supplier takes before storing finished products.
Random sampling is the third key element.
Your quality service provider pulls random samples and inspects them.
The random samples indicate whether the supplier has complied with your standards and specification.
Your supplier inspects the random samples by checking the packaging details and making sure the units produced conform to the golden standard you approved.
The final element of a robust product inspection strategy is the review of defects and writing a product inspection report.
Your inspector should take photographs of defects found.
Your inspector should also include these defects in their written report.
The inspector sends you the written report as feedback.
The report also contains recommendations and possible solutions to the quality issues and defects identified.
What is a Product Inspection Checklist?
A product inspection checklist is a criteria that your product inspector is expected to follow when inspecting your products.
The checklist also clarifies to your supplier the standards they are required to meet.
What does a Typical Production Inspection Checklist entail?
Sample checklist
A typical product inspection checklist entails a list of potential defects categorized as major, minor and critical.
Typical checklists also have; package and labelling sections, visual inspection sections, functional testing, special tests and carton-drop test sections.
What are the main Drawbacks of Product Inspection?
Product inspections add to the cost of production without adding value to the actual products.
An inspector’s fatigue may affect the results of the product inspection process.
Product inspection does not prevent the manufacture of defective products; it only serves to separate good quality products and defective products.
Can you conduct Product Inspection and Testing at the same time and place?
Yes.
You can conduct both product inspection and testing at your supplier’s premises.
You can choose to test the golden sample your supplier provides you with before mass production begins.
You can also choose to test sample units once your supplier begins mass production.
However, it is advisable that you do not rely on your supplier’s facilities to conduct testing.
Not all suppliers have certified laboratories.
The results obtained from uncertified laboratories are not accurate.
Your supplier’s internal staff is in charge of internal testing.
Internal staff may give biased test results to protect their employer’s interests.
They may also cover up defects to protect their employer.
How do Product Inspectors Classify Quality Defects?
Your own standards and requirements will determine how quality defects will be qualified.
Product quality inspectors base classification of defects on your acceptable quality limits (AQL).
Product inspectors qualify quality defects as minor, major or critical.
Product inspectors determine where to categorize defects based on the severity of the defects in question.
Why is Defect Classification Important during Product Inspection?
Defect classification determines whether goods pass or fail product inspections.
Therefore, considering the quantity and severity of possible defects helps you make informed decisions before shipping.
Who sets the Tolerance for Quality Defects?
Quality Control professionals suggest tolerable quality defects.
However, it is up to you as the buyer to set the tolerance for your products’ quality defects.
How do you decide Tolerance for Product Defects?
You decide your tolerance for product defects by making an exhaustive list of defects that are common with your product type.
You can then set your acceptance quality levels (AQL) with your exhaustive list of possible defects as a guide.
Your AQL determines whether defects minor, major or critical.
A defect is minor if it does not affect a product’s merchantability.
A product with minor defects is sellable, and customers will not have reason to return such products.
Examples of minor defects include slight variations in a product’s colour or light scratches that are hardly noticeable.
A defect is major if it renders a product unsellable.
Products with major defects will likely trigger returns by customers.
Major defects are hard to miss.
A defect is critical if using the defective product can cause injury or death.
Products with major defects should immediately fail inspection.
How do I address Defects with my Products?
Ask the manufacturer/supplier to correct any quality issues by either reworking the defective products or producing replacements.
You can re-inspect the products to ensure that the defects have been dealt with.
Destroy any unmerchantable goods to prevent them from reaching your customers.
Charge your supplier for any quality issues, if this is a condition that you have set as part of your agreement with the supplier.
What is a Golden Sample?
A golden sample is the final product sample that you as the customer approve before your supplier begins the mass production.
You get to know whether your supplier understands your standards and expectations by examining a golden sample.
Why is a Golden Sample Important in Product Inspection?
A golden sample shows that your supplier has complied with your product standards and expectations.
The golden sample gives you an opportunity to review the manufacturer.
You review your supplier’s capabilities based on the golden standard’s quality.
Golden samples ensure that your supplier does not cut corners to lower production costs.
The supplier cannot use materials of lower quality.
This is because the golden sample already set out what you expect the supplier to deliver.
Golden samples show that no more product revisions need to be carried out.
Therefore, they prevent quality defects before mass production begins.
Golden samples also ensure that your final product is of good quality.
When should I request a Golden Sample for Inspection?
You should request a golden sample for inspection before mass production begins.
You can also decide to ask for golden samples from multiple suppliers/manufacturers before settling on which supplier to work with.
What is an AQL inspection standard, and why is it such an important consideration?
An Acceptable Quality Level (AQL) is the minimum level of quality that a shipment is required to meet for you to accept it.
Quality inspection agents check random samples against your AQL.
If your inspector determines that the product’s quality levels are not acceptable, your supplier has to locate and rectify the areas in the production process that are causing these defects.
You can use an AQL to assess the quality of your product without having to visit your supplier’s factory to inspect the product.
You also save money and time while using an AQL because you do not have to inspect more goods than necessary.
What is a Product Inspection Report?
A product inspection report is the feedback that your Quality Control service provider gives you after conducting an inspection.
The product inspection report determines whether your supplier has to take any corrective measures with regard to product defects.
What does a Product Inspection Report look like?
Sample report
A product inspection report has descriptions of inspection dates, locations and the conditions of factories.
The report also lists the inspected products and defects identified.
This includes photographs of the products in question.
Product inspection reports also contain pass or fail recommendations from the product inspector.
What will I do with the report from the Product Inspection Company?
Product inspection defects only provide information on the level of defects found.
The report does not contain possible solutions to these quality issues.
You should share the report from the product inspection company with your supplier.
The supplier then reviews the report and makes improvements where necessary.
You should also give feedback to your quality service providers.
Besides, you have to understand the report and discuss areas you feel fall short of your expectations.
Your feedback will help you get accurate and satisfactory results from your service provider in future.
How do I get a Product Inspection Report?
You get a product inspection report when an inspection company performs product inspections.
Each time a product inspection is completed, the product inspector gives feedback on the sample lot inspected.
You can also ask for a sample report from your quality service provider.
The sample will help you get a better idea of what to expect from a product inspection report.
What is the Lead-time for receiving Product Inspection Report?
This is the amount of time necessary to carry out product inspections.
The amount of time needed to inspect goods varies depending on the type of product and manufacturing processes in question.
Some inspectors require a couple of days to complete and send you a report, while other inspectors are able to send a report a few hours after the inspection.
What should I do if the Production Inspection finds Defects?
Your reaction to finding defects depends on the extent of problems found.
If the defects are minor, you may decide to accept the shipment as is.
If the defects found are substantial, you may have the supplier correct or replace defective products.
You can also decide to cancel the entire order, depending on the extent of defects found.
What happens if my Supplier will not fix Product Quality Issues?
If your supplier fails to fix product quality issues, you can accept only the products without defects.
You can also choose to cancel the order entirely.
However, this option has several repercussions.
Your agreement with the supplier may include penalties for terminating the order.
This may cause you to strain financially, or even disrupt your business.
How do you choose a Product Inspector?
Product Inspectors
You consider the amount of money you will have to use, including the expenses involved.
You have to understand, however, that only considering costs when choosing a quality service provider is risky.
Quality service providers who charge low fees may also provide substandard services.
You also have to consider the level of urgency.
How soon do you want the product inspection done?
Are you in a position to wait for foreign inspectors to conduct the inspection or will local product investors do just fine?
You also have to consider whether you want full-time or part time inspectors.
You should also consider the level of experience a product inspector has with regard to your product type.
How do I know if my Supplier Supports Product Quality Inspections?
You know that your supplier supports quality inspections if they have no problem with you bringing in 3rd party inspector to carry out inspections.
Also, you know that your supplier supports product quality if he/she accepts accountability for quality related issues.
If your supplier admits to mistakes and quickly works to rectify defects, it shows that the supplier supports quality inspections.
Should I inform my Supplier about an Impending Product Inspection?
Yes.
It is important to inform your supplier that you intend to have a third party carry out product inspections.
Product inspectors have to schedule inspections at the supplier’s convenience.
This is why it is important to notify your supplier of your intention to have an independent 3rd party inspector to check the goods on your behalf.
Your supplier also handles your product with care when you tell them that you intend to carry out product inspections. Your supplier wants to build and retain customer loyalty.
They will take every necessary step to make sure that every step in the production process is done according to your standards and expectations.
How do I book a Product Inspection Service?
First, you have to send all relevant information to your quality service provider.
This includes the purchase order, known defects for the product in question, the inspection type required and the supplier’s address.
You then introduce the supplier to your quality service provider, especially if it is a new supplier who has no history with your quality service provider.
You then have to receive a booking form, arrange the inspection and set a date for the inspection.
How much Time in Advance should I book a Quality Inspection service?
You should book a quality inspection service well in advance to avoid delays.
Booking inspections early ensures the process is completed ahead of the scheduled shipping date.
Booking quality inspection services in advance also ensures that your quality service provider takes all your needs into account.
You should deliver your quality control checklist in advance so that your quality service provider prepares adequately for the inspection.
The checklist helps your quality service provider determine which tools to carry, in case special tools are required for the inspection.
Should I do Product Inspection on every Order?
Yes.
It is important to carry out inspections on every order because not all orders will meet your standards and requirements.
How do I Prepare for a Product Inspection?
You should first receive a golden sample from your supplier.
You then have to approve the golden sample.
The approval of a golden sample helps your supplier determine your acceptable standards and requirements.
You should then develop a quality control checklist.
The checklist helps your inspector understand what you expect to be checked.
You then inform your supplier that you intend to have a product inspection carried out by an independent third party.
How much is a Product Inspection Service?
Fees for product inspection services vary.
Quality service providers charge different fees.
Your quality service provider’s location determines how much the product inspection service will cost you.
If inspection staff is located close to the supplier’s factory, you spend less on travel costs.
If your quality service providers do not have their inspection staff spread out, you have to bear more travel costs.
For example, you may have to pay for their flights if they are located far away from your supplier.
You have to consider whether you want full time, part time or contracted product inspectors.
Your choice will determine the amount of money you have to pay for product inspection services. You have to pay full time and part time product inspectors salaries or retainers.
Retainers are paid either annually or bi-annually.
Contracted investigators are hired periodically.
They are hired when quality service providers do not want to pay staff salaries to inspectors who are only required to work when the need arises.
How do I pay for Product Inspection Services?
You have to determine your cost for inspection.
However, you cannot let cost be the only factor to consider when choosing a quality service provider.
Product inspectors who are cheap to hire may not provide thorough or reliable inspections.
You have to consider your quality service provider’s person-day rates.
Person-days are the length of time quality service providers spend in the field.
Most third party quality service providers base their bills on person-days.
A person-day includes the time your inspector needs to:
- Travel to your supplier’s location
- Randomly sample products and inspect them, comparing the products with your acceptable quality limits.
- Identify defective products.
- Write up an inspection report indicating their findings.
- Travel from your supplier’s location.
You should also take note of travel expenses.
Some quality service providers require separate fees for travel expenses, while others include travel expenses in their person-day rates.
How do I prevent Integrity Issues during Product Inspection?
You can prevent integrity issues during product inspections by exchanging your product inspectors regularly.
Relying on the same product inspector can put you at risk.
The inspector may bond with your supplier or the supplier’s employees.
Your inspector bonding with the supplier may make the inspector lenient.
You should not rely on your supplier’s internal quality control staff.
Internal quality control staff may be biased.
Time and monetary constraints may also cause the internal staff to carry out substandard inspection.
Why can’t I let the supplier do the Product inspection?
You cannot let the supplier carry out product inspection because internal quality control staff may be biased and fail to accurately report on the product inspection process.
Suppliers may not have your best interests at heart.
Some suppliers are only interested in shipping products out quickly to make money.
Their quality control staffs, eager to reach the bottom-line, carries out substandard product inspection.
The supplier’s quality control staff rarely provides you with detailed inspection reports.
You may end up paying for and receiving goods with unexpected defects.
When you receive damaged goods, the lack of an inspection report makes it difficult for you to determine whether such damage occurred during packaging or in transit.
That’s it – everything you need to know about product quality inspection.
However, in case you have any question or inquiry, BanSar team is here to help – contact us now.